How Job Cuts Are a Factor in Calculating GMP Compliance Risk
Plan for GMP Implications of Job Cuts
Stretched regulatory resources are driving a shift towards risk-based inspections. To help regulators, the PIC/S drafted a document warning inspectors to be wary of the GMP implications of job cuts.
“Significant changes in the number of personnel at a site are also useful to consider from a risk perspective during the review phases because... they may mean that there are fewer quality assurance resources available at the site,” the PIC/S stated. They further warned that such job cuts can lead to compliance problems later on.
It seems common sense that regulators could respond to a significant shift in headcount by raising the risk level of a production site. This would result in the manufacturing facility being inspected more often or changing the scope of the next GMP compliance audit visit.
Information about headcount changes is one of four factors that can prompt a review of a plant’s compliance risk. The other factors are information on quality defects, changes to manufacturing authorizations and a company’s report in response to its most recent inspection.
Three Rules for Decreasing Your GMP Compliance Risk
Since organizational change is a fact of life, here are some simple, common-sense rules that are, unfortunately, not currently common practice.
1. Invest in Intelligent, Organized Succession Planning
Firstly, let’s look at an example of poor planning. During a recent site visit, the production manager had only been in the position for one week. His induction program, in true ‘Sitting by Nellie’ fashion, took only seven days. From that point onwards, he was the lead, nervously signing batch records and doing the very best he could under difficult circumstances.
Changes to people’s roles and responsibilities are often accompanied by increases in error rates, reworks and the like. Risks can be reduced by investing in education, not just training. On our human error prevention course, we talk about learning new ways of working and how difficult it is to break old habits. New ways of working are learned and strengthened over months, not weeks.
2. Identify and Address What You Don’t Know
In our experience many companies survive on what we call “heroic management,” particularly management and supervision at the operational sharp end; those who work incredibly long hours completing tasks that often aren’t mentioned anywhere in the job description. When planning organizational changes, ensure you have a full understanding of the jobs and tasks that people do in addition to their job description. You will be amazed at the discrepancies that surface.
3. Invest in On-going Training and Education
Succession planning is only possible when you have a well-educated workforce. Underpinning expertise in products and processes provides you with the flexibility to move people around with greater confidence. Succession planning without proper investment in on-going training and education is an explosive combination. Companies who have invested in our quality leadership programs, whether in-house or residential, are now way ahead of their competitors. They have people with expert knowledge of quality systems, risk-based decision making and products and processes. They are better prepared to respond to the challenges of the future, including robust succession planning.
Talk to Us Today
Our team of experts works with companies around the world to prepare them for inspections by regulatory authorities and on remediation projects. Complete the form below and start a conversation today with one of our experts.
Source:
www.outsourcing-pharma.com/Article/2012/02/21/Job-cuts-a-factor-in-calculating-GMP-compliance-risk-PIC-S
How NSF Can Help You
Get in touch to find out how we can help you and your business thrive.
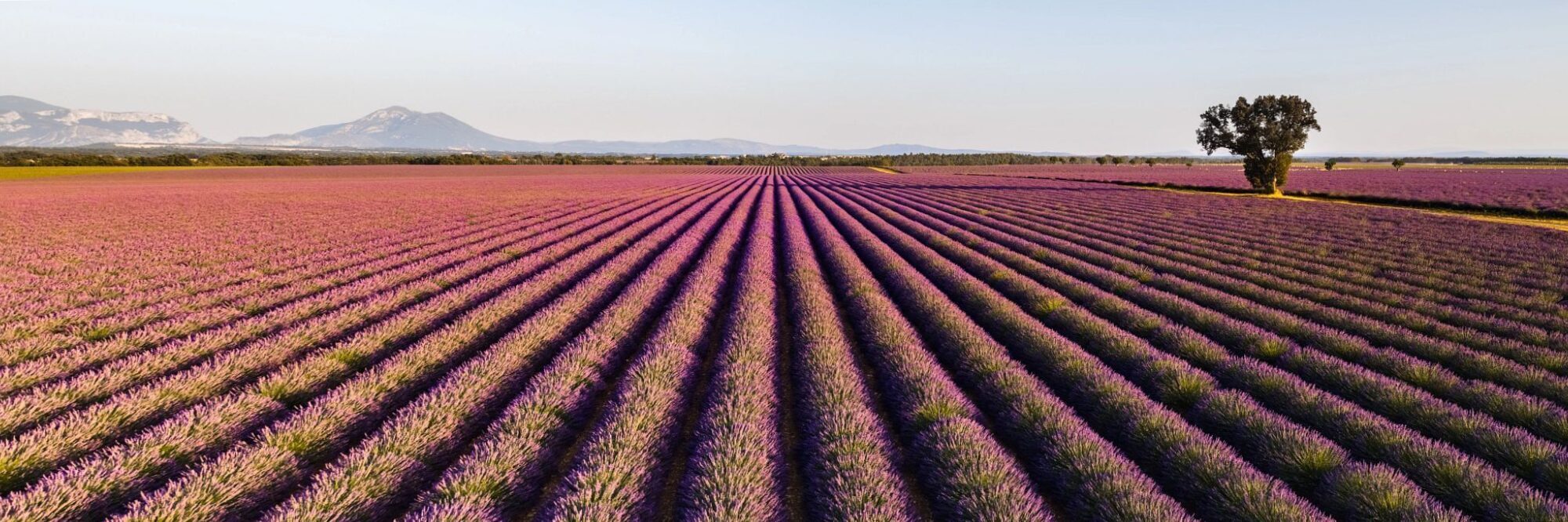
What’s New with NSF
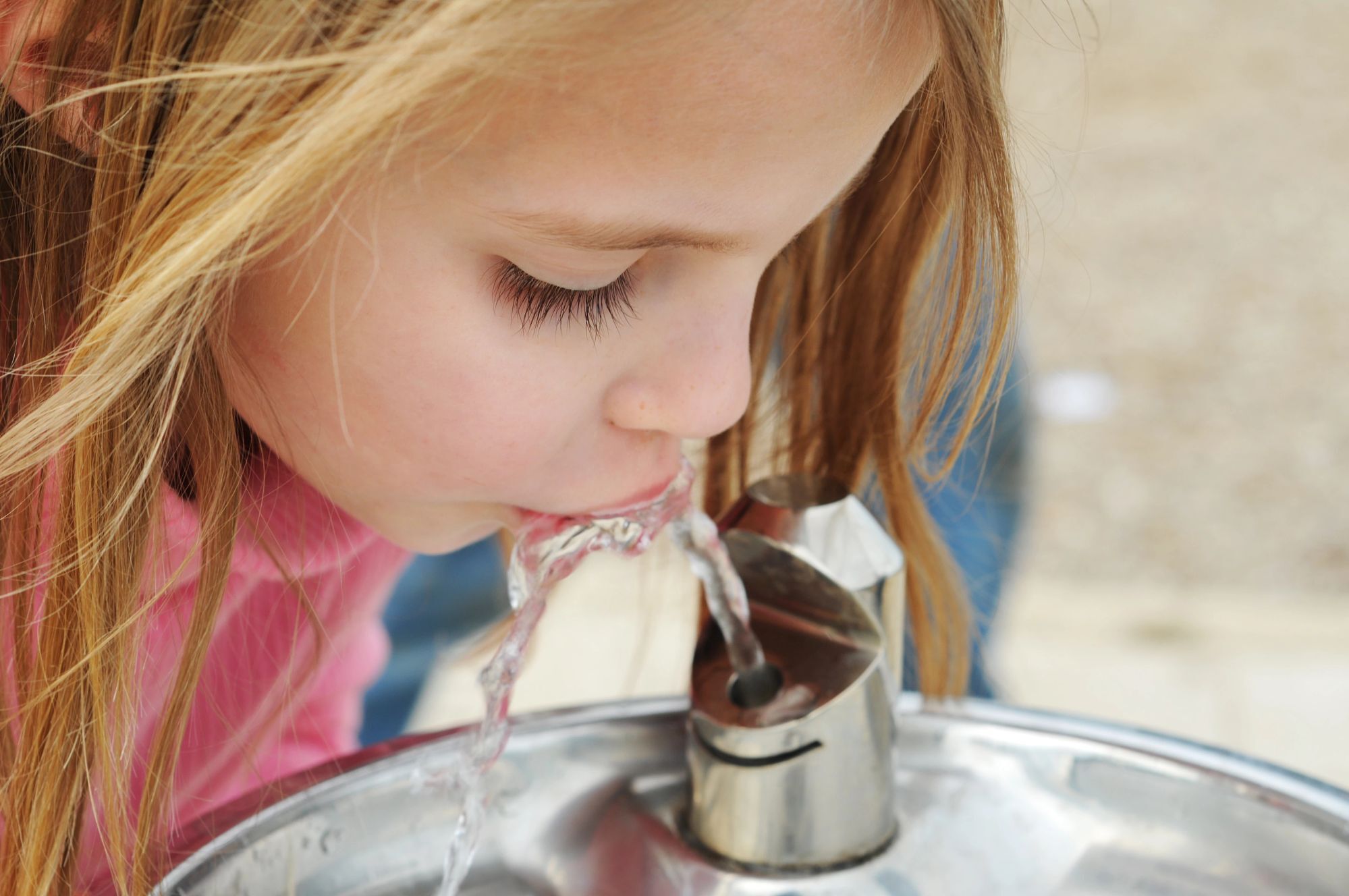
Michigan’s “Filter First” Law: A Guide for Schools and Childcare Centers
April 23, 2024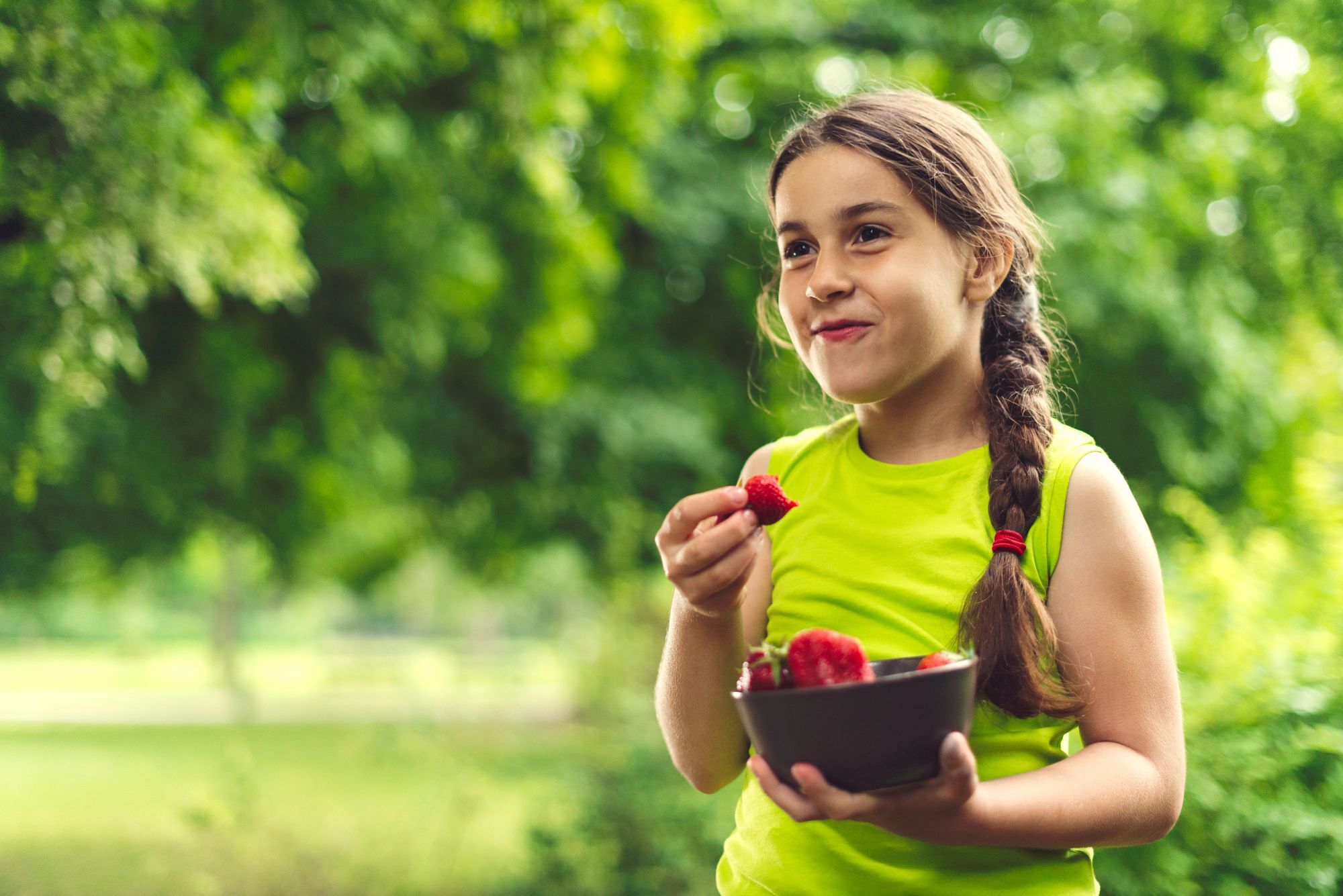
Healthy People Living on a Healthy Planet: The Future We’re Working For
April 4, 2024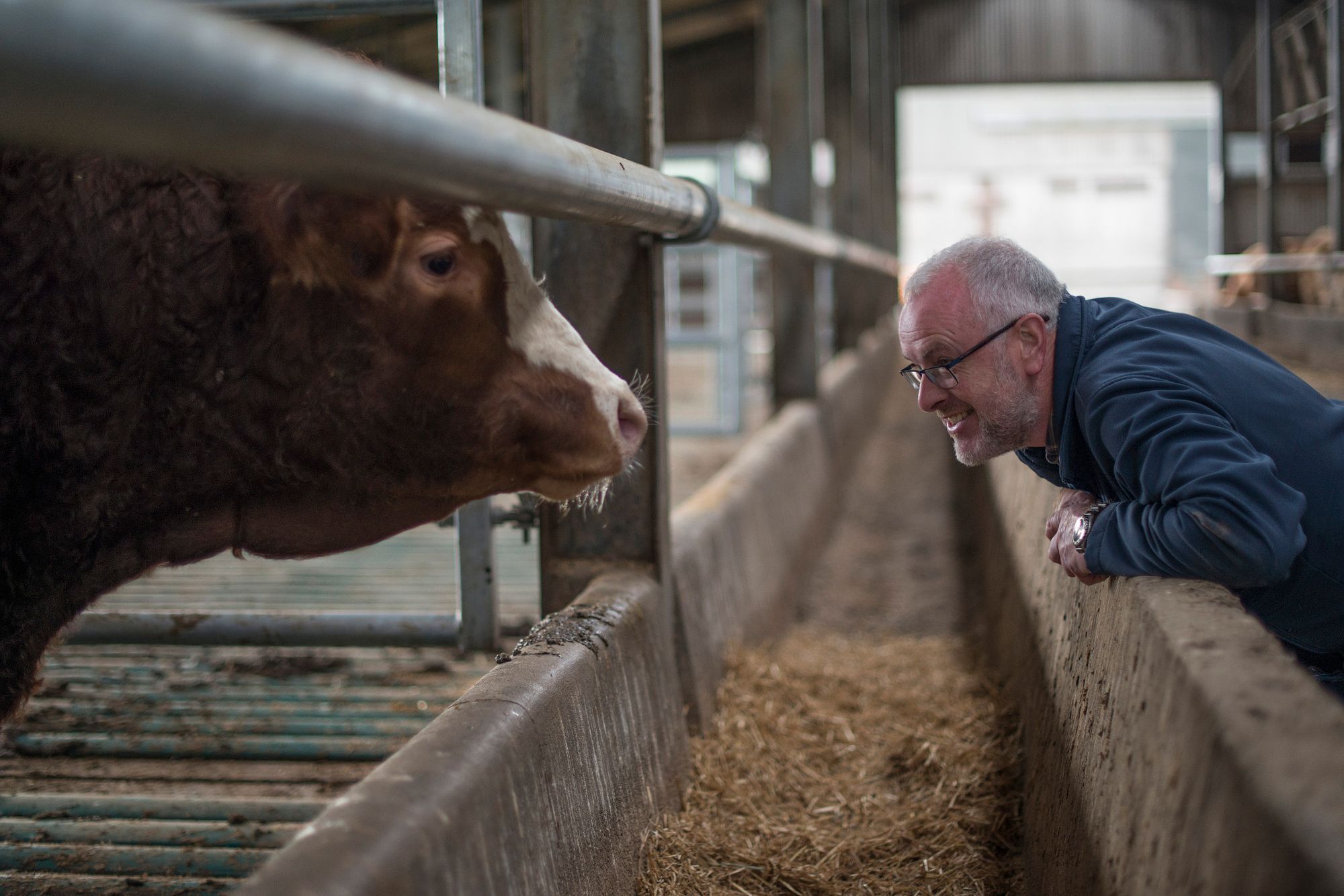
American Meat and Egg Distributors Now California-Ready with NSF’s Prop 12 Certification
April 3, 2024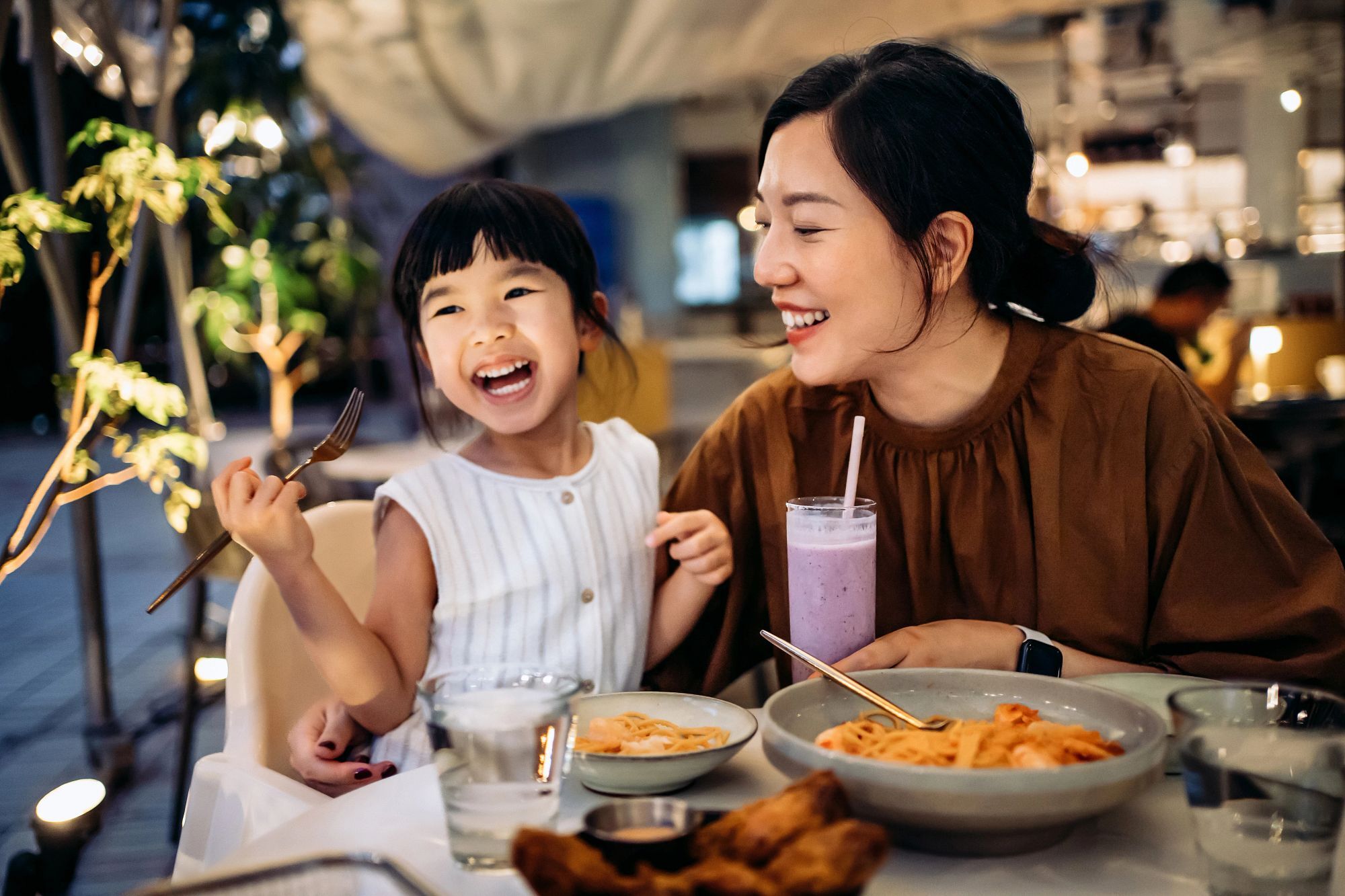